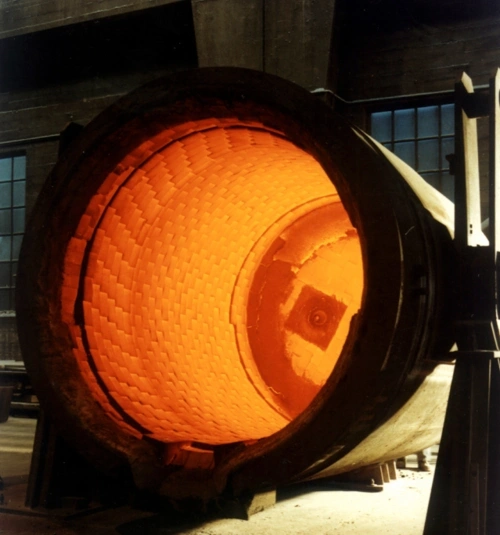
Critical Influencing Factors
1. Thermal Stress Conditions
Temperature Impact:
• Steel temperature directly correlates with refractory wear (1640-1690℃ operational range)
• Thermal cycling during baking→tapping→refining→casting creates significant thermal stress
Resultant effects:
- 30-50% increase in crack propagation rate
- Accelerated structural spalling in porous components like purging plugs
2. Slag Interaction
Multidimensional Slag Effects:
|| Basic Slag (CaO/SiO₂>2) || Acid Slag (CaO/SiO₂<1) ||
| Penetration Depth | 15-20mm | 8-12mm |
| Corrosion Rate | 0.8-1.2mm/heat | 0.3-0.5mm/heat |
| Viscosity Impact | Low viscosity→Deep penetration | High viscosity→Surface erosion |
3. Gas Purging Effects
Argon stirring demonstrates dual effects:
• Beneficial: Reduces pO₂ by 40-60% (protecting carbon-containing materials)
• Detrimental: Increases slag-refractory interface turbulence by 25%
Secondary Influencing Factors
Vacuum degassing: Increases refractory thermal shock frequency
Residence time: Prolonged contact (>150min) accelerates chemical wear
Mechanical stress: Ladle transportation induces structural fatigue
NC Refractory Technical Solutions
- 28 Years Specialized Manufacturing Experience
- Al₂O₃-MgO-C bricks with nano-scale pore structure
- Gradient-designed purging plugs (5-layer structure)
- Self-repairing castables with spinel phase regeneration